Single Hole Electrode Tubes vs. Multi-Channel Electrode Tubes
Another variable which ultimately determines successful EDM hole burning through a material or work piece is whether the brass electrode or copper electrode tube is has a single hole or multiple channels running directly through the ID or (Internal Diameter) of the electrode.
Basically, an electrode’s intended performance depends on the type of hole going through the center of the electrode, as different channel types are made for different purposes. One purpose is to direct water or coolant through the center of the electrode. This keeps the entire length of the brass or copper tube from overheating and burning up. If the electrode heats up too much it can soften and warp, thus preventing a straight drill or a consistent and accurate EDM hole.
The main factor that determines whether an EDM electrode tube would be single or multi-channel tube is whether the hole to be drilled is a through-hole or a blind hole. Blind holes are not drilled all the way through a workpiece, which leaves a slug or a nipple—a piece of material is still left untouched at the bottom of the hole.
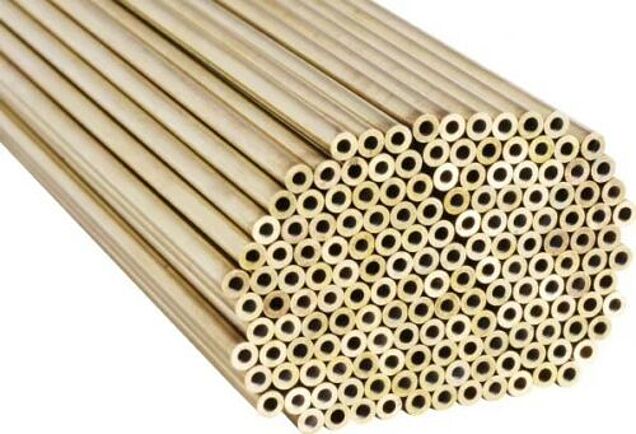
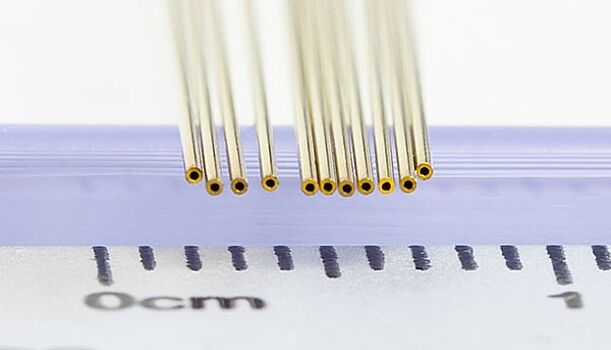
Brass EDM tubing and copper EDM tubing can both be single hole. Single hole electrodes are usually cheaper in price because there is less material in the electrode. Single hole tubing is recommended only for hole burning applications that require a hole to be drilled entirely through the part.
If you have further questions or would like clarification in regards to your machine, application or electrode type please email us or call us for further questions. We would be happy to help you and would appreciate any feedback you have to offer.
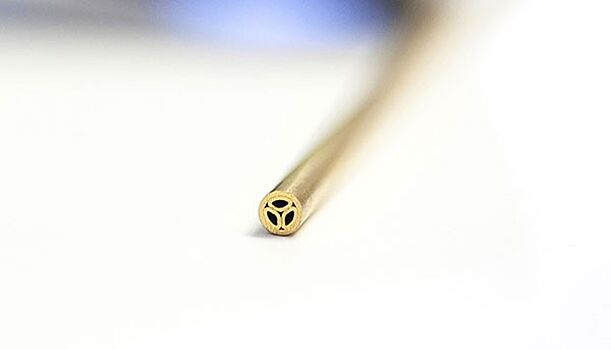
Multi-channel tubes are used for drilling a blind hole. The internal channels are designed to burn away any material left at the bottom of the hole, as the electrode has material inside the flushing hole that is used to disintegrate the work piece material.
The internal channels are arranged in such a way that, as the electrode spins, no part of the workpiece is left unaffected by the electrode, and no slug or piece of material is left at the bottom of the hole.
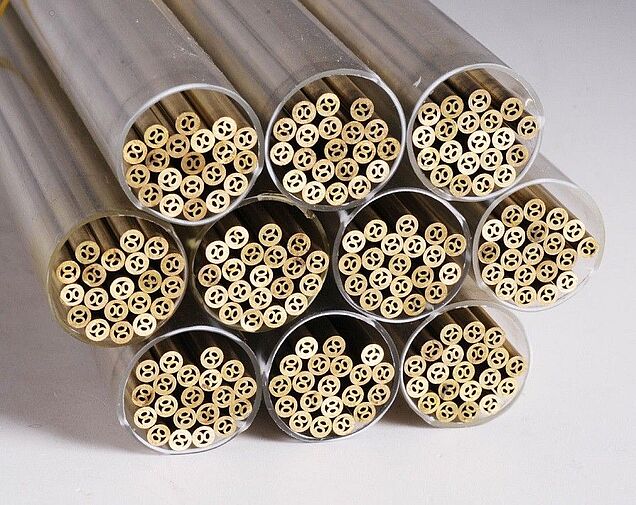