NOVICK® is revolutionizing die-sinking EDM with features like to be the most cost effective machine on the market, and patented technology to dramatically reduce electrode wear. Most of our die-sinking systems offer fast metal removal rates and deliver mirror finishes with pulse duration as short as 50 nanoseconds. NOVICK® Sinker EDMs feature latest energy saving technology. NOVICK® Die-Sinkers offer high speed and low electrode wear. They are high accuracy machines that produce fine finishes using Spark Machining
The Noviform-U is the most compact universal electrical discharge machine in the standard level segment
The new, modern machine design creates homogeneity with the entire Novick product range.
- High precision, high productivity machine stuffed with all features possible
- 3 axis cnc + optional C-axis + orbit II ® function + expert3 + DSAPCS pro
- Smallest increment 0.001mm, surface roughness achievable Ra = 0,14um with high mirror finish
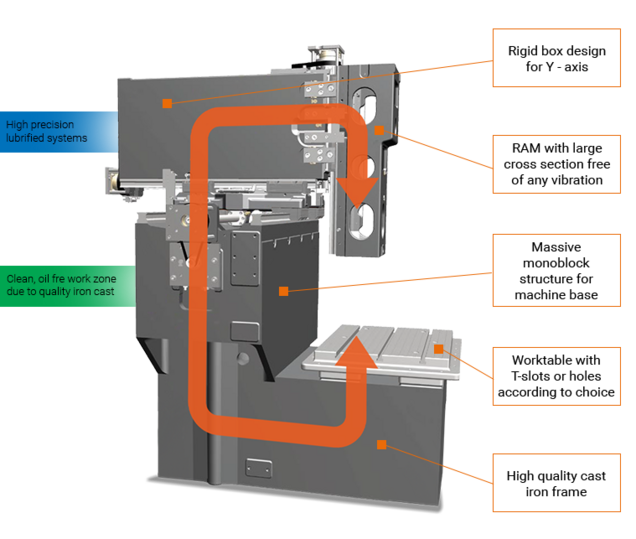
Why is our machine more stable?
Swiss C-frame design.
The mechanical design of the Novick machines is that of the fixed bench: combining robustness and accuracy.
The part to be machined rests directly on the independent fixed table of the meehanite casted vibration absorbing main frame.
This design, where the part is static, enables very heavy parts to be loaded without affecting accuracy. The precision components of the machine are used solely to move the electrode guides. Protected from dirt, shocks and stresses, they work permanently in an ideal situation to ensure durable accuracy. The fixed bench combines robustness and accuracy and keep all moving high precision components above and out of the working zone.
Traditional Swiss design and Japan based manufacturing techniques create machines where the performances of it do not change even after years of use. This longevity is due, to a great extent, to the manufacturing quality.
The very high accuracy surface grinding of the guiding and mounting surfaces contributes to this durable accuracy.
Before it is delivered, each machine is subjected to a laser test, which checks, in accordance with the VDI 3441 standard, that on all the axes positioning accuracy is situated within the specified tolerances.
Our C-frame beats them all!
Stronger, cleaner, more stable, more precise, less problems, higher load, ...
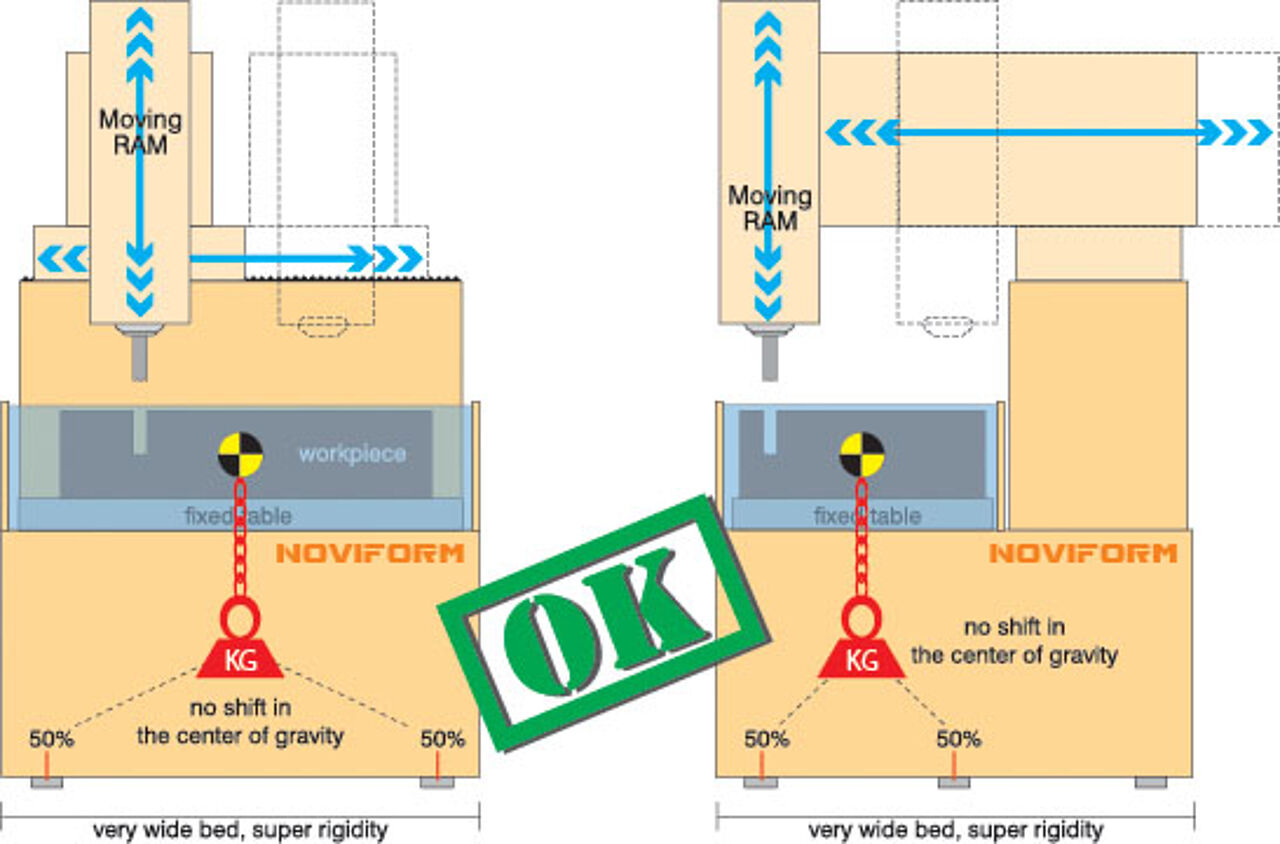
Do you want this in your workshop?
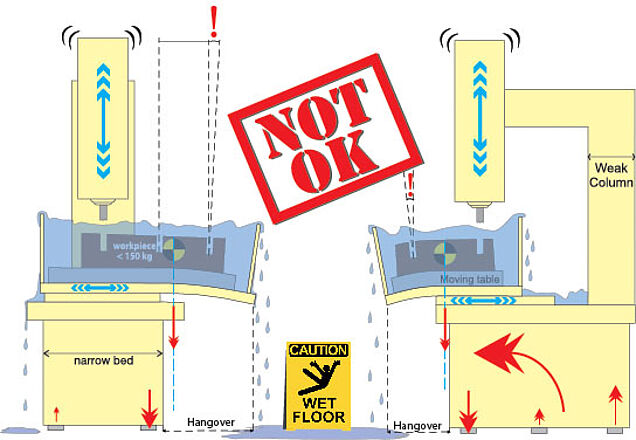
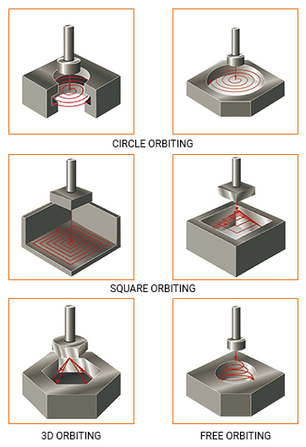
Orbit-II Pro-technology
Every Noviform® Die sinker is boosted with the new OrbitII Pro-technology providing higher machining precision and superior surface quality Noviform®Orbit II Pro Technology:
- Reduces machining time with 50% and electrode wear with 70%
- Improve surface finish quality with 50%
- Breaks through traditional restriction
- Upgrades the accuracy of the products•Increases efficiency and productivity
- Easy with intelligent design
- Fully tested through shock and vibration testing•Cuts at 45° for corner-sharpening
- Makes it easy to engrave a T-type channel
- Preventing build-ups of debris and deformation in boring a deep hole & big plane
- Hexagon machining
- 100% of Screw Mould Junction
- Different sizes of cavity machining can be done using just one size of electrode
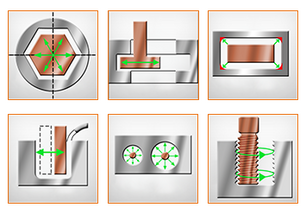
Orbit-II-Pro makes the difference
Conventional orbital machining (Spherical Orbiting or planetary movement of the electrode) is done consecutively, from point to point, along the targetedshape and the electrode movement is not smooth,resulting in unstable machining. The spherical orbitpattern is an option found on many advanced CNC sinkers. Spherical orbit patterns are not possible with mechanical orbiters or many of the available electronicspindle-mounted orbiters.
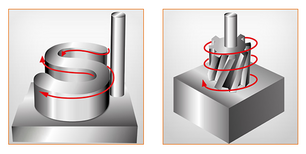
Contour-orbiting and C-axis orbiting
With our newly developed second generation Orbit II Pro technology, machining is done withan electrode that is in constant motion, following the targeted shape. This results in highly stable machining. The newly developed Orbit II Profunction smoothly guides electrode movement for uniform surfaces without unevenness. This advanced machining technology, in which the electrode is in motion continuously, results in stable finish machining with improved precision and quality.
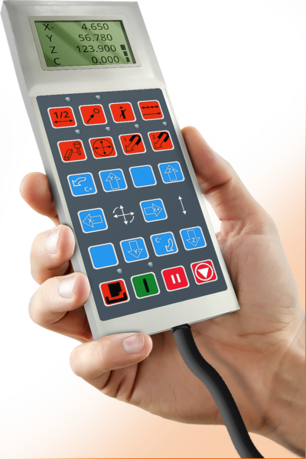
Portable Hand-controller with position display
Positioning with the electronic handwheel – Delicate axis traverse
Particularly with the portable handcontroller you are always close to the action, enjoy a close-up view of the setup process, and can control the infeed responsively and precisely.
The portable handcontroller with axis position display is particularly helpful for when you have to work close to the machine’s working space. The axis keys and certain functional keys are integrated in the housing. In this way you can switch axes and set up the machine at any time— regardless of where you happen to be standing. If you no longer need the handwheel, just attach it to the machine somewhere by its built-in magnets.
Dimensions and layout
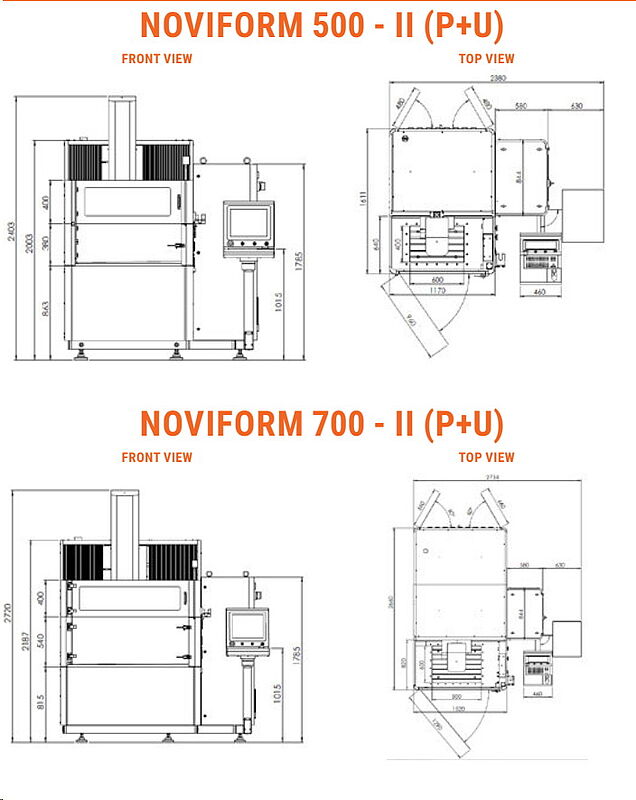