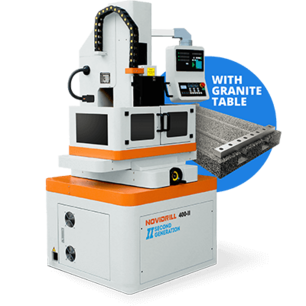
Tips for buying an EDM drilling machine!
EDM drilling can increase dramatically a shop’s capability
- Look for an EDM system that is fast, reliable and simple to operate. It should have enhanced drilling capabilities for extremely small hole sizes, but at the same time maintain good surface finish quality and accuracy at greater depths. Considering some of to-day’s applications, it’s important to look for a system that can drill a 15-mm deep hole as small as 0,20 mm in diameter in hardened steel and at the same moment to be able to drill a cooling hole of 2,5 mm in diameter 250-mm deep in mould steel, and this with minute variations in size and straightness from its entrance to exit.
- Most experts recommend selecting an EDM drilling system that utilizes the latest in digital generator technology. Digital generator technology, gives EDM drilling machines more precise spark control. It is this functionality that also helps reduce electrode wear. For optimal productivity, the goal is to generate as many holes as possible or drill as deep as required using the least quantity of electrodes. Thus, the more a generator can help reduce electrode wear the better. Plus, less wear on electrodes allows them to cut faster and more accurately by eliminating the “bullet nosing” of their electrode tips.
- Seek out an EDM drilling system that can be operated by any person in the workshop, without any high-level programming skills. Simplicity is here the rule.
- High-quality surface finish capability is a must. A growing amount of shops now use EDM drilling machines for generating finished holes that will not require any secondary finishing operations.
- Keep in mind that uneven wear increases a drilling electrode’s tendency to “walk” off centre, resulting in crooked and angled holes instead of straight ones. Because they help reduce wear, Supper high pressure coolant/flushing system thus prevent such a scenario and contribute to producing straighter holes and ones that can be held closer to size from top to bottom. For instance, a 200 mm-deep hole drilled with a 1 mm electrode on a digital generator-equipped EDM system will vary in size from top to bottom, usually less than 0,025 mm.
- Find an EDM drilling system that provides control over heat-affected zones for generating surface finishes comparable to those typically attained using a wire-type EDM. Such surface finishes are possible only with a super high pressure coolant/flushing system with sufficient debit to take the heat immediately away from the working zone.
- High pressure dielectric fluid is one of the most important factors, which is usually supplied to the gap through the bore of tubular electrodes. The use of a pneumatic intensifier pump results in drilling parts up to 50% faster and with lower operating costs as much as 40%! Pneumatic activated high-pressure pumps produce 30% more pressure than a standard water jet pressure pump, resulting in a 40-50% increase in productivity for many materials. Compared to a water jet pump, typical operating pressures uses 30% less water, 30% less power, and up to 50% less electrode consumption, resulting in a 40% reduction in operating costs. Being green with energy does not only spare the nature but also your wallet.
- Request a non conductive table of high precision, by preference Granite. A work-table from granite offers big advantages:
- You can’t drill into the table
- table resist to corrosion of the dielectric liquid: doesn’t get rusty
- keeps the super precision and guarantees a better flatness
- parts cannot be welded to the table due to bad contact with table
Conclusion
Today’s technically advanced EDM drilling systems essentially put hole making accuracy in the technological hands of the machine tool. Modern EDM drilling systems dramatically increase a shop’s capability to consistently produce tiny holes that are even more accurate and with higher quality surface finishes.