Smart-Pro and Smart-S-PRO Series
Technical specifications:
Machine | UNIT | Smart-300 PRO* | Smart-450S PRO** | Smart-500S-PRO** |
---|---|---|---|---|
Work Table Size(L*W) | mm | 500*300 | 750*450 | 800*500 |
X Axis - travel | mm | 300 | 450 | 500 |
Y Axis - travel | mm | 200 | 350 | 400 |
Z Axis - travel | mm | 200 | 250 | 250 |
W-axis - Travel | mm | --- | 250 | 250 |
Work Tank Intemal Size (L*W*H) | mm | 870*570*320 | 1050*610*450 | 1150*690*480 |
Max.electrode Weight | kg | 50 | 75/100 | 75/100 |
Electric cabinet parameter and specification | Ampère | ECO-40AMP | ECO-40AMP | ECO-40AMP |
Cont/Max processing current | A | 30/40 (opt 60/80) | 30/40 (opt 60/80) | 30/40 (opt 60/80) |
Max Loading Of Worktable | kg | 400 | 600 | 800 |
Distrance From Electrode Plate To Work Table | mm | 320 - 520 | 20 - 700 | 260 - 760 |
Oil Tank Capacity | L | 400 | 500 | 550 |
Machine Weight | kg | 1350 | 1600 | 2200 |
External Dimension(L*W*H) | mm | 1560*1415*2320 | 1780*1410*2380 | 1900*1485*2450 |
* = Single stroke Z-axis | ||||
**= Double stroke Z-axis (S-type) |
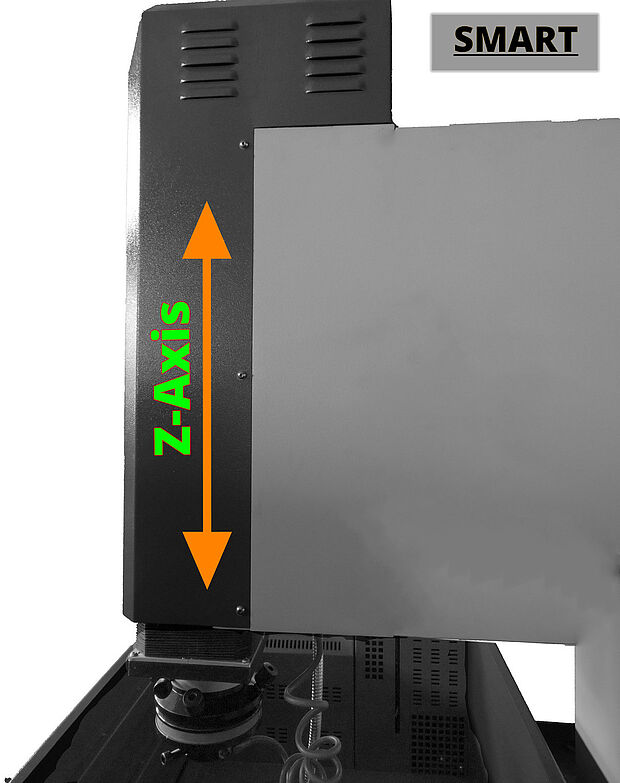
SMART- PRO Series
One Zaxis
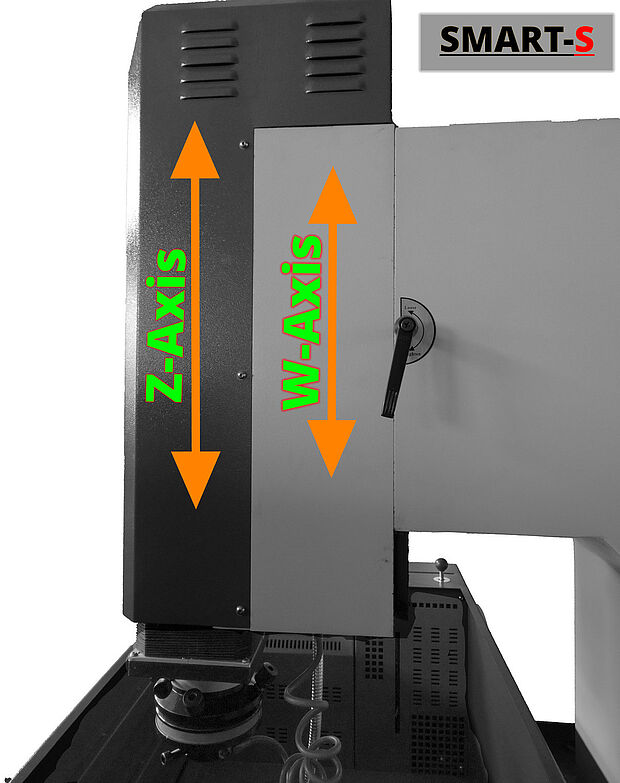
SMART-S-PRO Series
One Z-axis and One W-axis
Double length Z-axis stroke
Machine Meticulous Manufactured
High Standard Quality Control
Stiffness and precision are hallmarks of the new NOVIFORM SMART-PRO units. State-of-the-art methods have been used in their development, while the finest of modern machining and assembly techniques have gone into their construction.
Each machine is verified with a laser that checks the positioning of each axis to make sure it meets the norm of VDI 3441. Also, each machine must comply with the restrictions according to ISO 230-4.
- Compact space-saving design with integral dielectric system and generator for machining of small and medium-size parts
- X/Y axis use High grade Class of ball screw to keep easy transmission and high accuracy.
- Machine casting use strong material and season cast iron to release of casting inner strain to keep machine body high rigidity without bending.
- Machine construction according computer tensile strength, resist compression and stiffness strain.
- CNC controlled feed on X-Y-Z axis
- Integral design with compact footprint
- Precision co-ordinate table with needle roller bearings on symmetric guideways
- Highly accurate work head with the quill running on pre-loaded cross roller bearings
- Two-door, large work tank for ease of loading and unloading of the workpiece
- Rigid machine bed made of high-quality cast-iron
- Linear scales in all axes to ensure constant precision
- Di-electric tank integrated in the machine frame
- Manual central lubrication for table guides and spindles
- Servo drive on Z axis for fine-tuning of system stability
- User-friendly, easy to learn operation
- Parameters are entered directly at the control panel and can easily be optimized
- A lot of sets with positions and amperages or finishing steps can be entered
- Full safety interlock s including standard infrared &heat detector
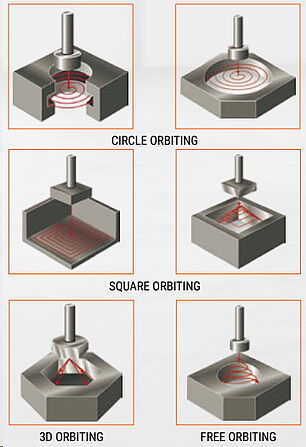
Orbit-III Pro-technology
Every Novick® Smart-PRO Die sinker is boosted with the new Fully integrated Orbit III Pro-technology providing higher machining precision and superior surface quality
Novick® Orbit III Pro Technology
- Reduces machining time with 50% and electrode wear with 70%
- Improve surface finish quality with 50%
- Breaks through traditional restriction
- Upgrades the accuracy of the products
- Increases efficiency and productivity
- Easy with intelligent design
- Fully tested through shock and vibration testing
- Orbiting in novick is possible in the 3 axis fields (in xy + z, xz+y and yz+x)
Novick® New CNC Orbiting-Cut System on our Smart-PRO Machines
Conventional orbital machining (Spherical Orbiting or planetary movement of the electrode) is done consecutively, from point to point, along the targeted shape and the electrode movement is not smooth, resulting in some less stable machining. The spherical orbit pattern we use is an option foffering many advantages.
With our newly developed third generation Orbit III Pro technology, machining is done with an electrode that is in constant motion, following the targeted shape. This results in highly stable machining. The newly developed Orbit III Pro function smoothly guides electro-de movement for uniform surfaces without unevenness. This advanced machining technology, in which the electrode is in motion continuously, results in stable finish machining with improved precision and quality.
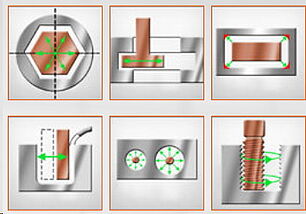
Orbit-III-Pro makes the difference
Conventional orbital machining (Spherical Orbiting or planetary movement of the electrode) is done consecutively, from point to point, along the targetedshape and the electrode movement is not smooth,resulting in unstable machining. The spherical orbitpattern is an option found on many advanced CNC sinkers. Spherical orbit patterns are not possible with mechanical orbiters or many of the available electronicspindle-mounted orbiters.
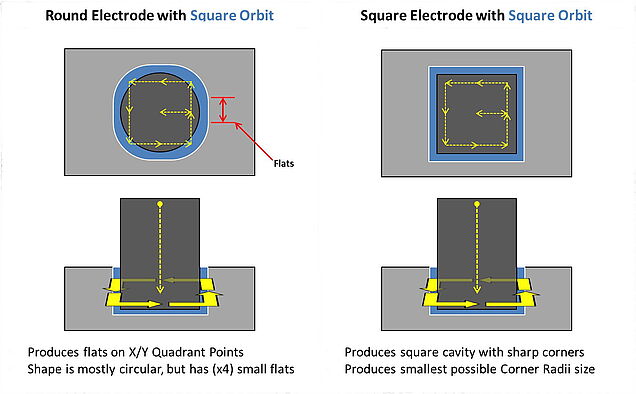
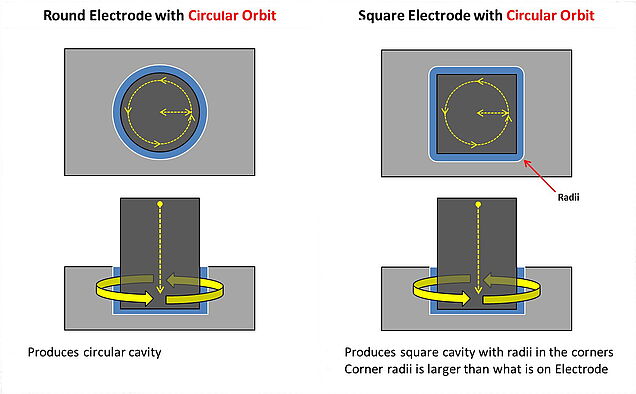
Download here your latest Catalogue of this machine!
Novick Catalogue download
Catalogue Noviform Smart Pro
Affordable quality Die sinking machine for every tool- and workshop